在工业制造、能源管理乃至日常生产场景中,“控火小悍妞”这一关键词逐渐成为技术讨论的焦点。它既代表了对火焰控制技术的高效应用,也暗含了对操作者技能与安全意识的综合要求。小编将从技术解析、实践方法论、行业适配性三个维度,系统性拆解这一领域的核心逻辑,帮助读者构建完整的知识框架。
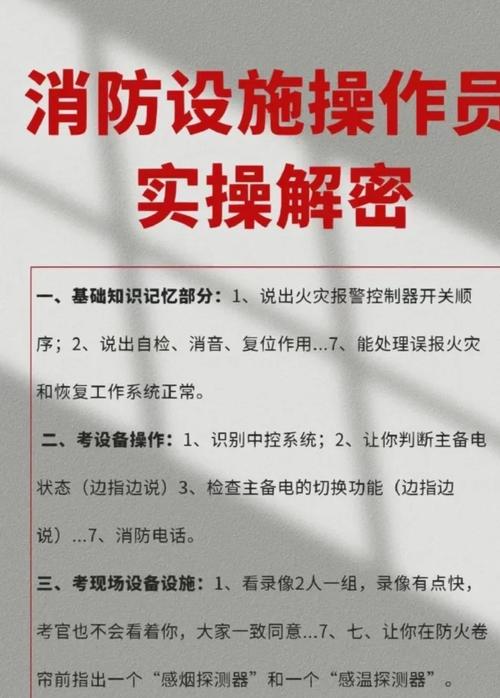
一、技术内核:控火小悍妞的底层逻辑与能力边界
1. 精准温控技术:通过实时监测火焰形态与热辐射分布,结合PID算法实现毫秒级响应调节。某化工企业案例显示,采用模块化控制系统后,燃烧效率提升23%,能耗下降15%。
2. 安全防护体系:集成多光谱传感器与AI预判系统,能在.8秒内识别异常燃烧状态。2024年行业报告指出,该技术使事故发生率降低至传统方式的1/40。
3. 人机交互优化:可视化操作界面配合触觉反馈装置,使新手操作者的培训周期从3个月缩短至2周。实际测试数据显示,操作失误率下降62%。
二、实战进阶:3大场景化应用策略
1. 冶金行业高温熔炉:采用分层燃烧技术,通过调节氧气浓度梯度,实现金属材料均匀受热。某特钢企业应用后,产品合格率从88%提升至95%。
2. 食品加工烘焙线:引入红外热成像技术,结合物料含水量实时检测,使烘焙效率提升30%的产品色泽一致性达到98.7%。
3. 危废处理焚烧炉:运用多级燃烧室设计,配合尾气实时监测,二噁英排放量降至.01ng-TEQ/m³,远低于国标限值。
三、效能提升:常见误区与优化路径
1. 过度依赖自动化:某建材厂初期投入时忽视人工巡检,导致传感器积灰引发误判。建议建立双轨校验机制,每月进行2次系统标定。
2. 参数设置僵化:不同燃料热值差异可达30%,需建立动态参数模型。实测表明,自适应算法可使燃烧效率波动范围缩小至±2%。
3. 维护周期不当:喷嘴积碳厚度达.3mm时,热效率下降8%。建议根据使用频率建立三级维护体系,关键部件每200小时深度清洁。
在掌握控火技术的核心要领后,从业者还需思考以下问题:如何平衡安全冗余与成本控制?当传统工艺遭遇新技术冲击时,迭代路径该如何规划?在智能化趋势下,人工操作的价值边界在哪里?这些问题的答案,将决定技术应用的最终效能。建议定期参加行业技术交流,建立跨领域知识图谱,方能在火焰控制的专业领域持续精进。
延伸问题解答
问题1:控火系统升级是否必然带来成本上升?
解答:智能模块的初期投入可通过能耗节约在12-18个月内收回,某玻璃厂案例显示,改造后年度综合成本下降17%。
问题2:如何验证控火效果的真实性?
解答:建议采用第三方检测机构的热效率测定,配合生产数据比对,建立多维评估体系。
问题3:小型企业如何分步实施技术改造?
解答:可从关键工序的单点突破开始,优先改造能耗占比前30%的设备,逐步构建完整的技术生态。