在工业自动化与电子设备控制领域,PPPD 287作为一种高性能控制模块,近年来逐渐成为行业关注的焦点。其独特的设计架构与稳定的运行性能,使其在复杂系统集成中展现出显著优势。小编将从技术原理、实际应用及用户常见疑问三个维度,深入剖析这一设备的核心价值。

一、PPPD 287的核心技术特性
1. 多协议兼容架构:支持Modbus、CANopen等主流工业通讯协议,实现与不同设备的无缝对接。通过智能信号转换技术,可适配超过20种传感器输入类型。
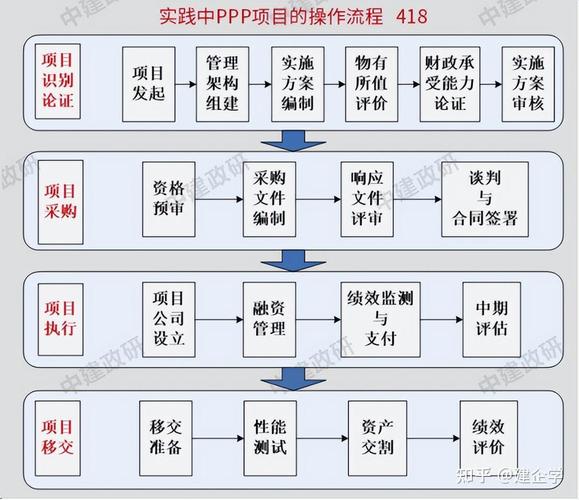
2. 动态负载均衡机制:内置的实时监测系统能自动分配运算资源,确保在突发性数据处理时保持响应速度低于50ms,避免系统卡顿。
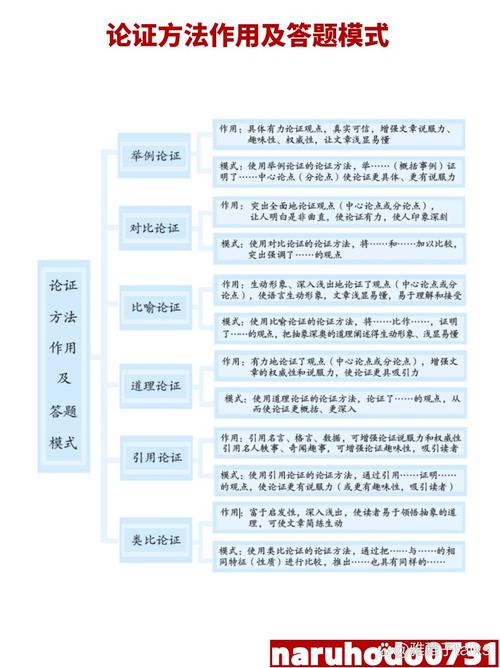
3. 环境适应性强化:采用IP67防护等级设计,工作温度范围覆盖-40℃至85℃,通过EMC四级抗干扰认证,满足严苛工业环境需求。
二、典型应用场景分析
在智能生产线控制系统中,PPPD 287常被用于以下场景:
1. 机械臂协同作业:通过16通道并行控制,实现多轴联动的精度误差控制在±.05mm范围内。
2. 能源管理系统:配合功率监测单元,可实时优化设备能耗,实践数据显示可降低整体能耗12-18%。
3. 远程运维支持:集成4G/WiFi双模通讯模块,支持OTA固件升级与故障诊断,显著提升设备维护效率。
三、用户常见问题解答
问题1:如何判断设备是否需要固件升级?
答:当控制面板指示灯呈现橙色闪烁状态,或通过配套软件检测到版本号低于V2.3.5时,建议进行升级操作。
问题2:模块支持的最大扩展单元数量是多少?
答:标准配置下可串联8个扩展单元,采用级联中继方案后最大支持32个设备组网。
问题3:异常震动环境下如何保证运行稳定性?
答:建议安装时使用专用减震支架,同时在参数设置中启用动态补偿功能,可有效消除5-200Hz范围内的机械振动影响。
随着工业4.技术的持续演进,PPPD 287的模块化设计理念正在推动控制系统的智能化转型。设备供应商提供的数据显示,采用该模块的生产线平均故障间隔时间(MTBF)提升至50000小时以上,为现代制造业的数字化转型提供了可靠的技术支撑。